Optimising service life with residual stress analysis
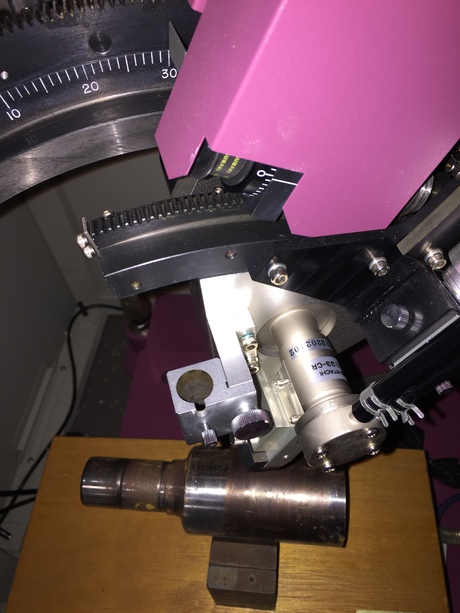
When it comes to X-ray analysis, one might think of techniques like XRD (X-ray diffraction), XRF (X-ray fluorescence) and radiography. However, another technique that uses X-rays is residual stress analysis.
Residual stresses are those stresses that remain in a material after the cause of the externally applied loads/stresses has been removed. These causes may be from the forming process such as rolling, forging or machining. Depending on the specific application, the residual stress may be advantageous or deleterious.
Residential stress expert Scientia Professor Liangchi Zhang is currently based at the University of New South Wales, but his career has previously taken him from China to the UK and Japan. During his time in Japan, he had worked with a Rigaku residual stress analyser. He then acquired a similar instrument, a Rigaku PSPC/MSF rapid stress analyser, to conduct research in Australia.
Processes such as grinding can have an effect on residual stresses and impact such things as mould tolerances. In a study with international industrial collaborators, Professor Zhang published results showing that processes such as surface and plunge grinding, and the resultant heat generated, can affect the properties of a hardened surface. However, with an understanding of the grinding process, it can be used to generate a hard surface with compressive residual stresses, leading to optimal service performance.
“Our Rigaku stress analyser is an excellent tool for measuring surface residual stresses,” said Professor Zhang. “It is ideally suited to metal forming and processing and looking at stress distributions in the resultant components.”
The rapid stress analyser is easily able to cater for small, medium and large samples with a range of different frame sizes. It also produces data quickly thanks to the Position Sensitive Proportional Counter (PSPC) and the fact that the system can collect data across the entire length of the sample simultaneously. These features make it suitable for catering for a range of industrial clients who produce such things as gears, rollers for the steel industry, punches, aircraft components, rails and wheels for trains, and pistons and cylinders for automotive applications.
“In most cases, compressive stresses in surface and subsurface regions will increase the service life of a component,” Professor Zhang said. “By looking at the relationship between processing parameters and the residual stresses induced in the components, we can optimise the processing conditions to produce a component that will ultimately last longer.”
Phone: 02 9450 1359
Pi Imaging SPAD Alpha high-performance single-photon camera
SPAD Alpha by Pi Imaging is a photon-counting camera for high-speed imaging and is suitable for...
Iconeus One functional ultrasound system
Iconeus's functional ultrasound (fUS) technology affords neuroscience and preclinical...
Confocal.nl NL5+ line-scanning confocal system
The NL5+ confocal system provides high-contrast images from thicker specimens such as organoids,...