Gas dosing control for microalgae facility
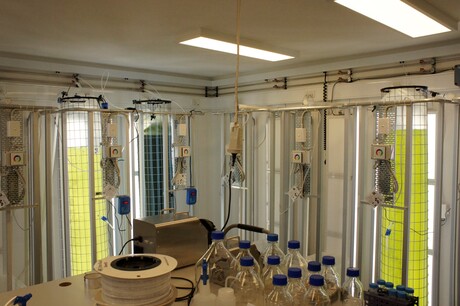
The Centre for Solar Biotechnology at The University of Queensland (UQ) was established in 2016 by Professor Ben Hankamer with the aim of accelerating the innovation and commercialisation of new solar-powered technologies and industries, many of which are based on photosynthetic green algae.
The centre operates both indoor and outdoor pilot-scale production facilities for micro- and macro-algae, which are equipped to operate high rate ponds, flat panel, tubular and airlift systems. This includes the testing of various bioreactor designs and process parameters, as well as testing and characterisation of production strains. Extensive infrastructure is already in place, including CO2 and compressed air with associated piping and automation technologies for the operation of the bioreactors.
The existing control system for the outdoor bioreactors had been built almost 15 years ago, and the centre faced an expensive upgrade option. As a result, UQ commissioned DSI Tec to upgrade the plant with a new control system. Together they designed a new control and monitoring system for the bioreactors, which includes pH-controlled CO2 dosing and remote sensor calibration capabilities.
DSI Tec explored a number of options and providers for mass flow meters and controllers, and other necessary equipment, but kept coming back to Bürkert. So Bürkert invited David Horton, Principal of DSI Tec, to the company’s Sydney Systemhaus to discuss the project in detail.
Specific valves and instrumentation were required for the control system, and the laboratory wanted a customised design that needed to communicate with a Siemens S7-1200 platform, using a Profinet network already onsite. The control system also required futureproofing and the design needed to allow for future upgrades with additional devices.
The first requirement was to provide a transmitter for eight raw pH probes. For this task, Bürkert supplied two of the Bürkert MultiCELL Type 8691, each with Profinet and four pH modules. The pH reading, as well as other diagnostic data, is sent directly to the Profinet network for monitoring and control.
The second requirement was to provide five multifunction controllers (MFCs) to dose air, with the capacity for an additional 20 MFCs to be connected in the future. To accommodate future expansion, Bürkert supplied five of its MFCs on its Efficient Device Integration Platform (EDIP). This offers a modular design to allow the addition of devices according to application requirements. Bürkert’s ME43 gateway device configured for Profinet provides an interface to the control system.
The third requirement was to provide solenoid valves for CO2 dosing. To this end Bürkert supplied a stainless steel manifold and valve system. The manifold was built in-house by Bürkert Australia and mounted on a stainless steel top-hat, which supports easy mounting and serviceability. The five valves are controlled directly from the Siemens PLC digital outputs.
“The challenge for Bürkert was to accommodate the tight allocated installation space onsite,” said Dean Bryant, National Segment Manager, Micro Fluidics & Gas Handling for Bürkert Fluid Control Systems. “We therefore provided a narrow, freestanding enclosure to accommodate all of the MFCs and valves.”
Bürkert readily provides control panels and cabinets as part of its solutions for ease of setting up systems in various locations. Bryant added, “The completed system included a Siemens S7-1200 PLC/HMI combination, which contained the Profinet Master that communicated with the other devices through Bürkert’s ME43 gateway device.”
The close collaboration between UQ, Bürkert and DSI Tec — from the conceptual design right through to installation — ensured that the project was delivered on time and on budget.
“The automation upgrade for the indoor production facility now enables a precise and remote control of microalgae cultures to produce high-quality biomass that is then used to develop bio-inspired green medicines, foods and nanomaterials,” said Dr Juliane Wolf, Research Officer and Project Manager. “Once we scale up the automation implementation further, to include our outdoor production facility, we can drive down the cost of production and expand the green developments to the production of fuels and ecosystem services.”
“Our indoor and outdoor pilot plants are critical to our work, and we thank DSI Tec and Bürkert for working so professionally and constructively to provide us with the automated control systems that we require,” Prof Hankamer said. “The system will take our R&D work to the next level of systems design and scale-up, so that we can provide the renewable products and jobs of the future through a solar-driven manufacturing base.”
Please follow us and share on Twitter and Facebook. You can also subscribe for FREE to our weekly newsletters and bimonthly magazine.
Phone: 1300 888 868
Dickson Smart DS intelligent sensors
The Dickson Company is releasing Smart DS — its second generation of intelligent sensors,...
HEMCO Vented Safety Enclosure (VSE)
HEMCO's Vented Safety Enclosure (VSE) is offered in 61, 91 and 122 cm widths to accommodate...
TOPTICA DL pro BFY tuneable diode laser
TOPTICA's DL pro BFY tuneable diode laser is especially suitable for applications where...