Electrostatic spray drying — manufacturing heat-sensitive biomaterials and special dairy ingredients
By Tiago Oliveira, Spraying System Co Pty – Fluid Air Australia, Melbourne, Australia.
Friday, 01 May, 2020
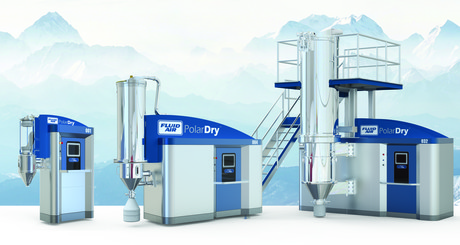
We can all agree that what makes us humans different from the other species coinhabiting this planet are mainly three facts: the ability of consciously thinking; the capability to create and change our surroundings; and our incredible aptitude to adapt.
Creativity and adaptation have been the key drivers of our evolution as a species and, in tough times like the ones we’re living in right now, demand us using our knowledge and innovation even further to solve the problems we face. Accepting the norm is no longer enough, we must find new ways to be safer, healthier, greener, more efficient and more sustainable.
With that in mind, Fluid Air, a division of Spraying Systems Co, has been promoting new manufacturing technologies for oral solid dosages within the pharmaceutical and food sectors around the world. Since its establishment in 1983, the company has been very successful in helping its customers to solve their problems and achieve their goals by implementing its range of products designed using novel technologies.
The newest technology developed by Fluid Air is the Electrostatic Spray Dryer – PolarDry®, a piece of equipment specially designed to fulfil a gap within the powder manufacturing marketing: the processing of heat-sensitive products in a continuous regime.
Until now, heat-sensitive materials were only able to be processed into a dry powder using two technologies: traditional spray drying, normally discarded based on the temperatures involved in this process (around 90°C final product temperature); or lyophilisation, popularly known as freeze drying, which normally requires longer processing times, presents limited throughput, requires further processing and allows some level of degradation on the final bioavailability of the material being processed. Although lyophilisation presents many challenges, this technology is broadly used in the pharma and food industry.
PolarDry, on the other hand, unifies the best of both worlds: the throughput and simplicity of a continuous process, with the ability to dry at much milder temperatures (30°C product temperature). PolarDry is the ideal solution for powder manufacturing of biomaterials such as microorganisms, anaerobic bacteria, probiotics, yeasts and dairy ingredients like colostrum, lactoferrin, infant formulas and non-bovine milk, among many other high-value products. Biomaterials dried using the PolarDry technology result in outstanding CFU counts, showing there are virtually no log losses involved in the drying process. Immunoglobulin G (IgG), T cells, antibodies and active lactoferrin levels present in the dairy product powders produced by PolarDry indicate higher values when compared with same materials dried using lyophilisation.
Throughout its complete range of electrostatic spray driers which covers everything from R&D and feasibility to small- and large-scale production, Fluid Air enables pharmaceutical and food producers to explore and develop new products with more effective formulations, diminishing heat degradation and decreasing oxidation while improving the stability and shelf life of the powders produced by its customers at a lower operational cost.
Fluid Air also acknowledges the importance of supporting its existing and future customers during their innovation and development phase; therefore, a range of laboratories has been built around the world to support customer trials and research using not only the PolarDry equipment but the whole range of Fluid Air solutions. To support the Australia and New Zealand markets, a state-of-the-art, fit-for-purpose, R&D ISO certified laboratory was built in Melbourne, enabling local customers to access this innovative approach in powder manufacturing. The Fluid Air Melbourne lab is not only equipped with a feasibility PolarDry spray dryer, but with all the major analytical equipment and some pre-processing apparatus necessary to emulate and validate the use of this technology in the industry.
Solving problems by using innovative solutions, being more efficient and developing new tools and techniques are some of the values entrenched into Fluid Air’s DNA. Through applying these values, Fluid Air aims to support the local industry and community, contributing to a cleaner, safer, greener and more sustainable society.
World First — Clever Engineering and Flexible Technology Solves a Nanoparticle Challenge
It is not every day that you get to solve a unique problem. But that's exactly what happened...
Ergonomic devices for pain-free pipetting
Pipette design has a significant influence over operator body position and force required while...
What if a Magical Lab Balance Granted Your Top Three Wishes?
High-resolution lab balances are critical for precision in pharmaceutical research, analytical...