A revolution in spray drying and microencapsulation
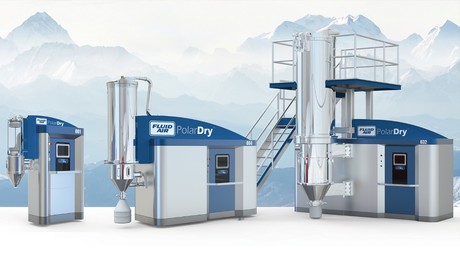
Designing a spray drying process for heat-sensitive products has always been a big challenge. Traditional spray dryer technology always made use of intense heat, which ended up damaging or decreasing the quality of the end product.
With this in mind the next big change in spray drying has reached the Australian and New Zealand market, the PolarDry™ Electrostatic Spray Dryer by Spraying Systems Co.
After years of development and refinement this new system is set to change the way many companies dry their product, making the process easier and more effective while no longer sacrificing your product’s end quality.
Low-temperature drying
Low-temperature drying is the technology that is set to change the way those in the pharmaceutical, food industries and more operate and think about spray drying.
In traditional drying there are two distinct phases: constant rate and falling rate. With the PolarDry system, the need for a falling rate period is negated due to its unique process. It utilises an electrostatic effect to stratify its components during atomisation. The solid materials are driven to the inside of the droplet with the solvent being expelled to the outskirts of the droplet. This allows for fast, efficient drying without raising the heat and damaging the product, while achieving higher micro encapsulation.
Traditional vs electrostatic microencapsulation
Utilising spray drying technology is not a new practice, with this method being used in many industries since the 19th century. Advancements have made this drying method more effective over time incrementally, with PolarDry being a significant jump in the technology and its effectiveness. Traditional encapsulation uses emulsion made up of a solvent, a carrier and a core. In this method the carrier remains the protective layer as the emulsion is atomised, with heated drying gas then introduced to the atomised emulsion. This high-temperature method can dry out the particle that has the active trapped inside the droplet and the surface, which can make this method ineffective.
The PolarDry system is different as it offers companies electrostatic technology that is the latest innovation in spray drying. By following this process near perfect encapsulation can be achieved without using high evaporation temperatures.
Two machines in one
PolarDry gives companies the ability to control electrostatic charge applied on an intermittent basis which is a means of agglomerating particles when dried. This feature called Pulse Width Modulation (PWM) does away with the need for expensive additional agglomeration operations.
Controlling the voltage applied to the droplet while atomised allows for two types of particles to form. One particle is wet or tacky, the other forming an outer shell readily, and when those combine they make the agglomerated particle. This process creates a finished product with larger particles and fewer fine lines.
Safety and flexibility are paramount
Like all products sold by Spraying Systems Co, the experts in spraying, safety is a primary concern. That’s why when we designed the revolutionary PolarDry System we made sure that the system includes a redundant oxygen monitor that prevents operation if the oxygen level is above 5%. The system also includes an emergency stop button and safety reset, to give your organisation peace of mind.
We also know that no two businesses are the same and need unique solutions to their specific products. That’s why we made every model we offer easy to set up from one run to the next no matter your requirements, with a disposable inner chamber liner that can be changed in only a few minutes. The cartridge filter configuration is also unique and features a reverse pulsing feature which ensures that drying gas flow remains steady.
Scalability
Process scalability is one of the main differences between this system and others which don’t allow your system to grow as your business does. PolarDry features as a modular design allowing for future growth capabilities without changing the whole set-up. These models range from easily portable to stationary, so no matter what size your operation is and where it is located, there is a system that can be matched to your company’s specific needs.
Find out more from the experts
Spraying Systems Co is celebrating over 80 years of global leadership as the world’s largest manufacturer of spray nozzles and spraying systems. We offer expert advice, best quality spray hardware and complete automated systems designed and engineered to suit almost all industry needs. Our sales engineers can assist you to improve your production, save money and improve your efficiency. Our Sales Engineers are strategically located servicing all states of Australia, New Zealand, New Caledonia and Papua New Guinea and can help you find out about PolarDry and more.
Talk to one of our PolarDry experts today and book a free on-site evaluation now.
Call 1300 958 878 or visit us at http://www.fluidairinc.com/AU/electrostatic_spraydryer.html.
World First — Clever Engineering and Flexible Technology Solves a Nanoparticle Challenge
It is not every day that you get to solve a unique problem. But that's exactly what happened...
Ergonomic devices for pain-free pipetting
Pipette design has a significant influence over operator body position and force required while...
What if a Magical Lab Balance Granted Your Top Three Wishes?
High-resolution lab balances are critical for precision in pharmaceutical research, analytical...