CFR data loggers for sterilisation and freeze-drying process validation and qualification
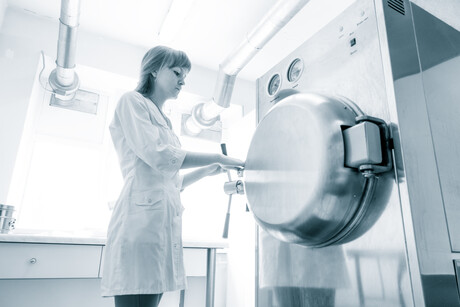
As health service organisations align themselves to the set of sterilisation standards published in 2016, the need for reliable validation technology is also in greater demand. The testo 190 is a state-of-the-art sterilisation data logger that provides support for validation and qualification tasks in laboratory environments. The system measures and monitors temperature and pressure in sterilisation and freeze-drying processes. Because of its simplicity and ingenuity, this technology is ideal for health service organisations.
The testo 190 is Testo’s premium temperature and pressure data logging technology that is ideal for the biomedical, medical, dental, and pharmaceutical industries. These specialist data loggers enable your operation to engage in robust sterilisation and validation protocols, whether in the hospital, pharmaceutical or biomedical laboratories, that would guarantee accurate data logging and readout results while being simple and easy to use. In addition, the logger has full, audit-relevant documentation that is accessible with just the click of a button.
You will find that the technology includes seamless and effective support for your validation and qualification tasks. From the simultaneous programming and readout of up to eight CFR data loggers at the same time, through comprehensive data analysis, to audit trail functions and digital signatures — the 21 CFR Part 11-compliant software is extremely simple to use.
The testo 190 all-in-one solution supports you with innovative data loggers, intuitive software, and practical accessories to meet these challenges. So, you can always rest assured that the qualification and validation of sterilisation, disinfection and freeze-drying processes will be carried out in an extremely efficient manner, in compliance with the standards.
Why you need it
Steam under pressure was first developed in 1679 when Denis Papin invented the steam ‘digester’, from which concept in the 19th and 20th century autoclaves have been developed, and has been used commonly ever since because it is the most reliable way to destroy microbes. The vapor released as pressurized steam raises the temperature, which kills viruses and germs. Effective autoclave sterilisation requires steam temperatures between 121 and 132°C and typical pressurisation is between 1.5 and 4 bar. In such severe conditions, it is important to have a high level of confidence in the reliability of the loggers and their accuracy.
This is where the trustworthy and simple-to-understand testo 190 CFR software comes in handy. Because the software is so easy to use, there is no need to spend extra time training people on how to use a complex system. Additionally, testo CFR software allowing for a readout of up to 254 loggers is possible in one validation process.
If you’re seeing wet sterilisation bags and materials after a cycle, your autoclave may be suffering from poor steam quality. Poor steam quality ruins an efficient workflow, and you may need to start the whole process over again. A quick and easy way to validate steam quality is with the use of an accurate autoclave logger that works in tandem with the testo 190 CFR software.
The testo 190 CFR software also has the following individual process parameters:
- temperature span
- minimum hold time
- maximum acclimatisation time
- lethality
- maintain GxP procedures
- supplies reliable audit trails
The parameters are explained in the software and are easier to understand because of this. At the same time, the testo 190 CFR software enables comprehensive analysis, graphical and tabular display and evaluation of all recorded measurement data.
The testo 190 is an innovative and industry leading technology that eliminates many issues before they appear. See the results of the testo 190 endurance test in our downloadable whitepaper and contact Testo for your technical enquiries.
World First — Clever Engineering and Flexible Technology Solves a Nanoparticle Challenge
It is not every day that you get to solve a unique problem. But that's exactly what happened...
Ergonomic devices for pain-free pipetting
Pipette design has a significant influence over operator body position and force required while...
What if a Magical Lab Balance Granted Your Top Three Wishes?
High-resolution lab balances are critical for precision in pharmaceutical research, analytical...